Efficient dispersing and mixing are essential for the production of high quality paper and board products and the runability of further production systems. GAW dispersing systems guarantee the required viscosities, solid contents and rheologic characteristics of homogenous dispersions and emulsions.
Top Drive System
GAW dispersing machines with topdrive systems are designed under the premises of energy efficiency, consistent and reproducible qualities, scalability, preservation of the medium and optimum process connection.
Dispersion Disc
The classic dispersing disc is ideal for simple dispersing and homogenizing tasks. The design of the toothed disc, the number of revolutions, and the positioning of the components within the containers, which are adapted to the respective application, ensure optimum results.
Rotor-Standard
GAW's top drive rotor standard dispersing machines enable the gentle preparation of simple product formulations. For more omplex applications, these dispersing machines can easily be retrofitted to the patented Combined Dispersing System (CDS).
Rotor-CDS 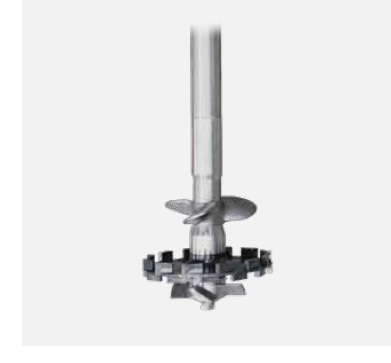
The patented GAW Combined Dispersing System enables the user to disperse difficult-to-process products at a high solids content, allowing for tremendous flexibility when it comes to recipe formulation. The CDS optimizes the entry of the dry product, reduces the use of dispersant and massively reduces energy consumption.
Rotor-Stator-Standard
GAW's Rotor-Stator standard dispersing machines are based on the basic principle of kinetic energy. The use of a rotor-stator unit ensures the forced dispersion of the product to be processed. The top and bottom propellers assist in delivering the media to the rotor-stator system, thereby providing optimum circulation in the dispersing vessel.
Rotor-Stator VST
The GAW Variable Shear Technology (VST) combines the advantages of the rotor-stator standard systems and dispersing toothed discs. VST is based on the stepless adjustment of the rotor-stator overlap during operation. This allows the user to set an optimal ratio between rotation and shear for all applications.
Bottom Drive System Suspendend Type
GAW bottom-drive dispersing machines are designed in a suspended or upright design.
Here, the design of the containers of the bottom-drive dispersing machines is adapted to the respective case of application. Options such as dosing monitoring, process temperature control via double-walled containers and connection of the GAW Quality Loop enable customers to achieve the desired qualities in a targeted manner.
Bottom Drive System Upright Type
The pneumatic baffle influences the circulation. It is controlled via pneumatic cylinder. In the lower position it ensures more efficient dispersion, in the upper position increased circulation in the container.
GAW bottom-drive dispersing machines are available in the low shear standard, high shear standard or Variable Shear Technology (VST) adjustment units.
Low-Shear-Standard
High-Shear-Standard
Variable-Shear-Technology (VST)
The Variable Shear Technology is based on continuous alignment of the shear rate during operation, thereby ensuring extremely careful and steady coating color processing.
Since dry products can be directly dispersed, higher solid contents are achieved than when using conventional systems and the binding agent and energy requirements are optimized.
Afterwards dispersion follows with high shear rates in combination with the VST with continuous adjustability up to 100 % coating. Input behaviour and shear rates can be adjusted on the one hand by means of the VST and on the other hand by the rotation speed during operation.
ContiMixer
The GAW ContiMixer is a continuous dispersing machine in which a large number of raw materials are processed into a coating mass.
In its maximum size CC750, the ContiMixer enables a throughput of up to 35,000 litres per hour, around the clock. Its special division into four different mixing zones prevents the heating of the coating medium and enables correspondingly high solids contents and viscosities. Since the ContiMixer is a completely closed system, impurities are eliminated and consistent colour quality is ensured.
Compared to the batch process, the continuous processing of coating compounds offers enormous advantages for the manufacturer.
Generally, the total cost of operation of the system is considerably reduced. Connected load and energy consumption are reduced by up to 75%, coating colour losses during recipe changes are avoided, and water consumption and maintenance costs are drastically reduced.
GAW dispersing units, the heart of the coating colour kitchen, are equipped with the latest dispersion units which allow the highest possible level of production quality.